某型商用车动力电池托架的轻量化设计 复材云集|复合材料
复合材料家具如衣柜,重量轻但耐用,省电冷却 #生活技巧# #居家生活技巧# #节省能源的生活习惯# #复合材料建材#
搜狐 新闻 体育 汽车 房产 旅游 教育 时尚 科技 财经 娱乐 更多 无障碍 搜狐汽车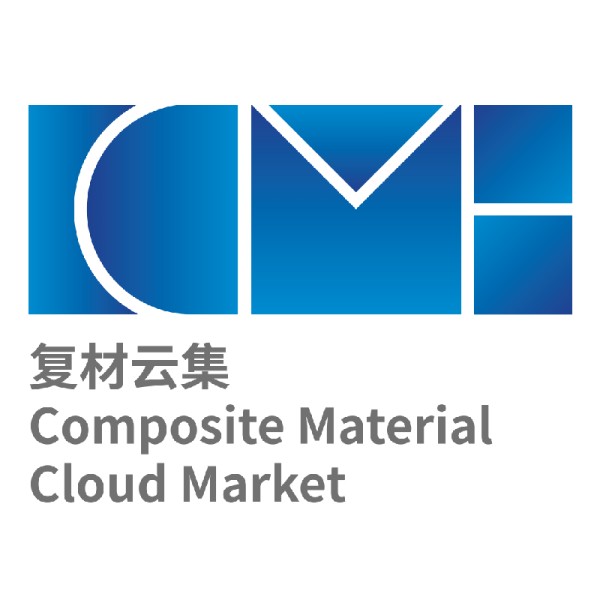
某型商用车动力电池托架的轻量化设计 复材云集|复合材料
在全球气候变暖以及能源危机的形势下,发展纯电动汽车成为世界各国节能减排的重要举措。纯电动汽车具有噪音小、能耗低、绿色环保的优点,已逐渐成为汽车行业中的热点,但是纯电动汽车的动力电池质量和体积较大,并且装载动力电池的托架也过于厚重,这极大地增加纯电动汽车的整体重量,而整备质量又是影响新能源汽车能耗极其重要的一个因素,因此,对动力电池托架进行轻量化的研究具有重要意义。动力电池托架是承载动力电池的主要结构,一方面其底部支架形成电池组冷却结构的底部风道,用以确保电池组工作在适当的温度范围内[1-2],另一方面它作为电池组的支撑结构,保证电池组在工作过程中始终安全可靠。本文来源于动力电池托架的实际生产,主要使用ANSYS Workbench进行有限元分析及结构优化,旨在以塑代钢实现动力电池托架的轻量化;同时确保托架的承载强度,保证纯电动汽车行驶的可靠性和安全性。
1 电池托架结构分析
1.1 电池托架结构形式
某型动力电池托架的总体尺寸长×宽×高=2430mm×935mm×1865mm,其外罩结构使用材料为ABS,现对内部金属材质结构进行优化改进。图1为动力电池托架内部结构图,材料采用结构钢Q235,为空心框架结构,质量为375kg。
图1 动力电池托架内部结构图
1.2 电池托架结构设计
使用通用塑料聚丙烯(PP)和工程塑料尼龙(PA6)及玻纤增强聚丙烯复合材料(PP+GF30)以塑代钢,材料主要性能见表1。
表1 材料性能特点对比
对原结构进行改进,采用分体式结构,上方采用方管和外壳相连,下方采用三角连接件和车架连接,连接方式均采用螺栓连接。由此设计出三种方案,见表2。
表2 三种结构方案
2 电池托架有限元分析
2.1 工况设置
动力电池质量约为1 740 kg,内部四个载物框架均受力4 350 N。由于电动车在实际行驶过程中通过的路面条件复杂,同时,动力电池托架在随电动汽车行驶过程中所受到的载荷并非直接来自于外界,而是来源于汽车制动、转弯、颠簸等状况下电池包对电池托架产生的惯性力。所以在研究动力电池托架静态受载时,为找出应力分布和位移变化,选取常见典型的极端工况进行分析。动力电池托架通常在汽车颠簸、急刹车等极端工况下的受载较为激烈。选用颠簸路面下的急刹车工况进行研究分析,各载荷参数见表3。
表3 载荷情况(g=9.8 m/s2)
2.2 有限元分析
当汽车行驶时,底部电池托架主要受自身重力作用的影响,其均匀施加在电池托架与动力电池组接触面上。通过ANSYS Workbench分析设置工况下的各材料托架的安全系数与位移,求解结果见表4。由表4可知方案一的结构性能最优,若采用PP和PA6,三种方案的结构安全系数都不能满足要求,而使用PP+GF30方案一和方案二都能满足使用要求,因此可以选定材料为PP+GF30,初步优选的结构为方案一和方案二。
表4 三种结构方案
3 电池托架结构优化
3.1 疲劳寿命分析
疲劳寿命分析的结果如图2所示,动力电池托架的疲劳寿命最低处均是在部分拐角处,两方案的结构区别在于两侧的支撑板,其寿命均在200万次以上。由于方案二的质量比方案一小,因此暂定结构为方案二,接下来对部分拐角处进行圆角处理。
3.2 结构优化设计
对方案二结构进行优化,对部分连接处进行圆角处理,将底部垫块对称安装,改进的结构及有限元分析结果见表5。可知改进后的结构最大位移小、结构刚度好,最小安全系数为1.23,疲劳寿命也满足要求。
图2 方案二疲劳分析结果
表5 结构优化后的有限元分析结果
3.3 拓扑优化
拓扑优化是在给定的设计区域内寻求最优材料分布的一种优化方法[3-4]。拓扑计算时,采用密度法(SIMP法),即将有限元模型设计空间的每个单元的单元密度作为设计变量,其计算方法如下所示:
K(ρ)=ρP k (1)
其中:K为惩罚刚度矩阵;k为实际刚度矩阵;ρ为材料密度;P为惩罚因子,P≥1。优化求解后,单元密度靠近1的位置材料很重要,需要保留;单元密度靠近0的位置材料可以去除,从而实现轻量化设计[5]。首先进行网格划分,如图3所示,然后指定规定材料和受力条件之后,结构优化结果见图4,表明深色区域可进行结构去除与轻量化改进,浅色区域不可进行结构改造,据此对结构进行轻量化改进。改进后的结构质量为272 kg,相较于原来使用结构钢的质量375 kg,实现了减重27%的效果。
图3 网格划分
图4 结构优化示意图
4 成型工艺分析
通过Moldflow对制件进行注塑成型模拟分析确定制件的最佳成型工艺方案,这有助于降低生产成本,提高设计效率。现以托架结构中受交变载荷为主的支撑板为例进行工艺分析。
充填过程中,注塑时间、流动速率、螺杆速度曲线是对填充进行控制的变量。在初次分析时,按默认选项“自动”进行填充分析,蓝色区域为浇口,结果见图5,可以看出在默认条件下无法充满型腔(图5(a)四个角有灰白区域),因此将注射压力提升到150 MPa,保压压力提升到90 MPa,可看出完全充满型腔(图5(b))。
图5 填充分析
设置冷却水道时各参数选定默认参数,冷却剂的出入口温差不应过大。图6所示为支撑板的平均温度结果图,可以看出温度分布较为均匀,只有在塑件拐角和型芯处出现最小温度,对整体结构影响不大,只需在模具设计过程中注意圆角的设计。
图6 零件平均温度
图7(a)为制件达到顶出温度的时间。顶出时间的差值应尽可能减小以实现均匀冷却。结果显然不符合要求,因此需要调整冷却管道直径、数量和中心距离,改进结果如图7(b)所示,顶出时间分布较均匀。
图7 达到顶出温度的时间
5 结论
动力电池托架材质上选用玻纤增强聚丙烯复合材料(PP+GF30),采用整体式、中心位置设置横向框架的结构,可实现相比原金属材质托架减重27%的效果。借助Moldflow进行注塑模拟分析,调整优化出了最佳成型工艺参数。
声明: 本文由入驻搜狐公众平台的作者撰写,除搜狐官方账号外,观点仅代表作者本人,不代表搜狐立场。
回首页看更多汽车资讯登录
请输入手机号 请输入右侧的数字/字母 请输入短信验证码 获取验证码下次自动登录
登录网址:某型商用车动力电池托架的轻量化设计 复材云集|复合材料 https://www.yuejiaxmz.com/news/view/426937
相关内容
手机屏损坏可“自愈”?自修复材料商用可期自修复材料商用可期,再也不用担心你的手机屏摔碎了
汽车内饰材料
复合材料行业用工业级无尘打磨设备
PC材料在新能源汽车领域的创新技术应用及趋势
汽车轻量化设计:为行业节能减排减负
自修复材料文献综述:研究、应用与前景
长安凯程品牌战略焕新:数智驱动,共绘新能源商用车新未来
装饰材料室内设计论文通用12篇
关于加快推动郑州制造业高质量发展提案的答复